Link to .pdf
Link to Seveso Inspection Series Home Page
MJV Good Practice Report
Process Safety Performance Indicators
Definition - Application - Purpose - Scope - Types of SPIs - Description of SPIs process - Techniques for evaluating SPIs - Communication of SPI results
This report aims to provide guidance for European Union (EU) Seveso inspectors on the use role of safety performance indicators, SPIs, that are commonly used by major hazard operators in the control of major risks and management of process safety. It provides a definition and explains the purpose of a safety performance indicator. It also describes the approaches to designing and selecting an SPI programme. It gives information on how the SPI programme can be implemented in order to remain a dynamic tool for monitoring the risk control system throughout the life of a chemical hazard site. It also includes references to the leading guidance produced by government and industry on developing and implementing effective safety performance measures.
Safety Performance Indicators (SPI) are referred to in Annex III of the EU Seveso III Directive within the issue of monitoring performance, that is, the ongoing assessment of compliance with the objectives set by the operator’s Major Accident Prevention Policy (MAPP) and safety management systems (SMS) and the mechanisms for taking corrective measures. The text of the Directive is clear that the use of SPIs is a possibility and not a binding requirement, and also that other relevant indicators may be useful. Examples of other indicators may be from occupational safety management systems, environmental management systems or integrity managements systems – the aim being to use existing information rather than unnecessarily generating new indicators. This sets the context for the purpose and application of SPIs in the context of Seveso Directive implementation and process safety in general. [6]
From 8-10 April 2018 the European Commission and the Austrian government hosted a workshop for Seveso inspectors targeted at achieving a clearer understanding of
- How SPIs are being used to monitor process safety performance in Seveso establishments
- Approaches to selecting and implementing SPIs and examples of what typical SPIs looks like
- Experiences of different Seveso inspection authorities on the use SPIs in enforcement and monitoring
This report summarises the current state of good practice emerging from the workshop exchanges.
1. Definition (what are SPIs?)
Several definitions of SPIs exist across industry but in broad terms SPIs are proxy measures for process safety which a major hazards operator would consider critical to the control and management of its major hazards. SPIs can be considered to form part of a safety management system which generally includes the following elements:
- A safety policy
- Organisational arrangements to support safety. This requires the coordination, selection, supervision and training of staff to support the safety policy and processes
- A safety plan. Standards and processes for safety, including using risk assessment
- A means of measuring safety performance. Processes and data are required to monitor current and past safety performance and anticipate that of the future
- A means of reviewing safety performance. This requires the assessment of safety performance against the safety objectives. This may involve processes such as incident investigation, safety surveys, audits and reviews as well as SPIs
- Feedback to improve safety performance. Mechanisms to ensure improvements are captured for and communicated to all relevant staff
It is worthwhile to point out that SPIs are not the only means of monitoring and reviewing safety performance. Conversely, SPIs will not address every aspect of safety related performance. As an analogy SPIs are neither a chosen destination nor the route to that destination but are signposts along the route.
2. Application (Who uses SPIs?)
SPIs originated with the hazardous industries, mainly oil and gas producers and chemical manufacturers. They are still largely developed by and for hazardous industry operators particularly multinational companies, but they may be equally useful in other hazardous industries and in downstream industries where significant chemical hazards are present in daily operations (e.g., used as fuel or for refrigeration). The degree to which inspection authorities encounter the use of SPIs on their Seveso sites can depend on the nature of the industries in their jurisdiction and the regulatory culture.
SPIs within the context of the Seveso III Directive are owned by the operator of the establishment. Generally, they should not be defined by external forces such as government agencies. It may however be beneficial to agree on a set of indicators which are shared with government inspectors to demonstrate the performance level of the SMS in question. As each MAPP and SMS should be specific to the operator and the establishment, the set of indicators which are developed will, in total, be specific to that establishment. [6] For example, SPIs have been developed by authorities with industry to address elevated risks from ageing infrastructure and to monitor risk control in the offshore oil industry.
3. Purpose (what do SPIs do?)
Over the last decade SPIs have been of increasing interest to operators because in several instances of major accidents, especially in the aftermath of Grangemouth in 2000 and Texas City in 2005, it has been found that the monitoring of process safety performance has been wrongly conflated with that of personal safety. Personal safety performance measurement is primarily focused on the negative outcomes of workplace incidents and illness. The most common way to identify these failures is the assessment of ‘lost-time injury frequency rates’ which measure the number of working hours or days lost through workplace injury and work-related illness. While the monitoring of injuries is clearly a necessary component of a safety management system there are several reasons for not relying too heavily on measures of injury to reflect the overall safety of a system. [6]
- Under-reporting. An emphasis on injury and ill-health rates as a measure, particularly when related to reward systems, can lead to such events not being reported to ‘maintain’ performance
- If an event results in an actual consequence (harm or damage) is often a matter of chance, so it will not necessarily reflect whether a hazard is under control
- An organisation can have a low injury rate because of luck or fewer people exposed, rather than because it manages health and safety effectively
- Lost time injuries can be used simply as a judgement of safety performance, rather than to understand the contributory factors and underlying causes behind the injury rate
And equally
- There is little proven correlation between personal safety statistics (such as slips, trip and falls) and control of major accident hazards (such as loss of containment of flammable or toxic material)
Several major accidents have occurred on sites which have enjoyed exemplary records in personal safety. Bearing all this in mind when it comes to process safety, SPIs seek to address the following key questions:
- Is the operator management of major hazards proportionate to the risk?
- Is the operator control of major hazards effective? (doing the right things)
- Is the operator control of major hazards reliable? (doing things right consistently)
- Is the operator getting better or worse over time?
- Does the operator have an effective safety management system in place across all parts of the organisation?
- Is the organisation supportive of process safety, particularly in the face of competing demands and significant organisational changes?
In addressing these key questions, SPIs should always align to the major accident scenarios which are outlined in the MAPP and described in a safety report. Furthermore, SPIs should be integrated into a safety management system so that they focus effectively and reliably on control of major hazards.
4. Scope (what do SPIs cover)
In terms of major hazards SPIs will cover those risks which the operator believes to be essential for satisfactory control of these hazards. Some of these will become apparent through operating experience and investigation of events such as accidents, losses of control, near misses and non-compliances. Other SPIs will be focused on the preservation of the basis of safety including engineering design, management of change and competency of operating staff.
It is not the ambition that performance indicators are set against all elements of all risk control systems on a complex installation, or that collection and analysis of data should be unnecessarily resource intensive. Neither is an overload of SPIs required. It is important to have a manageable number of carefully selected and targeted good quality SPIs to provide assurance across the whole business.
Specifically, SPIs should inform the operator of the Seveso establishment as to [6]:
- Whether the objectives of the MAPP are being reached;
- How well the individual procedures and processes are performing, e.g., are they being complied with, are they achieving the desired results
- Whether the mechanisms for taking corrective measures achieve their purpose, i. e., are deviations identified, are the underlying causes for deviations investigated and understood are appropriate corrective actions taken and communication processes initiated?
One specific aspect that is also mentioned in the Seveso Directive is the reporting, investigation and follow-up of major accidents and ‘near misses’.
It should therefore be clear that SPIs are an information tool. However, they are not the only information tool (others include accident reports, audit reports and other business performance documents) and care should be taken when establishing an SPI system that the indicators themselves do not become the purpose of the process.
5. Types of SPIs
SPIs can be considered to fall into two camps, lagging and leading (alternatively, outcome and activity) indicators.
Lagging SPIs are retrospective measures of failure and are useful for external benchmarking. Examples would include instances of losses of containment in terms of leaks and spills which could lead to hazardous effects such as fires, explosions and releases of toxic materials. Lagging indicators monitor the outputs from the process. Corrective action is taken if the outputs deviate from the required standard. The control is reactive, as corrective action cannot be initiated until the undesirable outputs have occurred.
In contrast, leading SPIs promote preventative actions before the hazard manifests as an incident and are useful for internal tracking of performance. They monitor inputs to safe operation before any adverse outcomes have occurred. Leading performance SPIs provide feedback early in the process and enable pro-active corrections to be made before any adverse outputs have resulted. To do this, performance standards are required for each of the inputs being measured.
Lagging SPIs inevitably represent a bottom line for safety performance, but clearly it would be absurd for a major hazards operator to rely entirely on lagging SPIs to understand its own safety performance. Simply waiting for disaster to strike is irresponsible. A more proactive approach is to both identify the major accident precursors and address these. Ideally, a combination of lagging and leading SPIs is desirable.
There are a number of approaches for selecting indicators so that the SPIs are effective for evaluation and improvement of safety performance. The tier-based and barrier approach are two of the most common approaches used, developed by the Center for Chemical Process Safety (CCPS) and the UK Health and Safety Executive (HSE), respectively.
5.1 The tier-approach
The tier-based approach is illustrated in the incident pyramid in Figure 1. According to this model, lagging indicators are associated with events closer to the top of the pyramid whereas leading indicators are associated with events or conditions towards the base.[3]
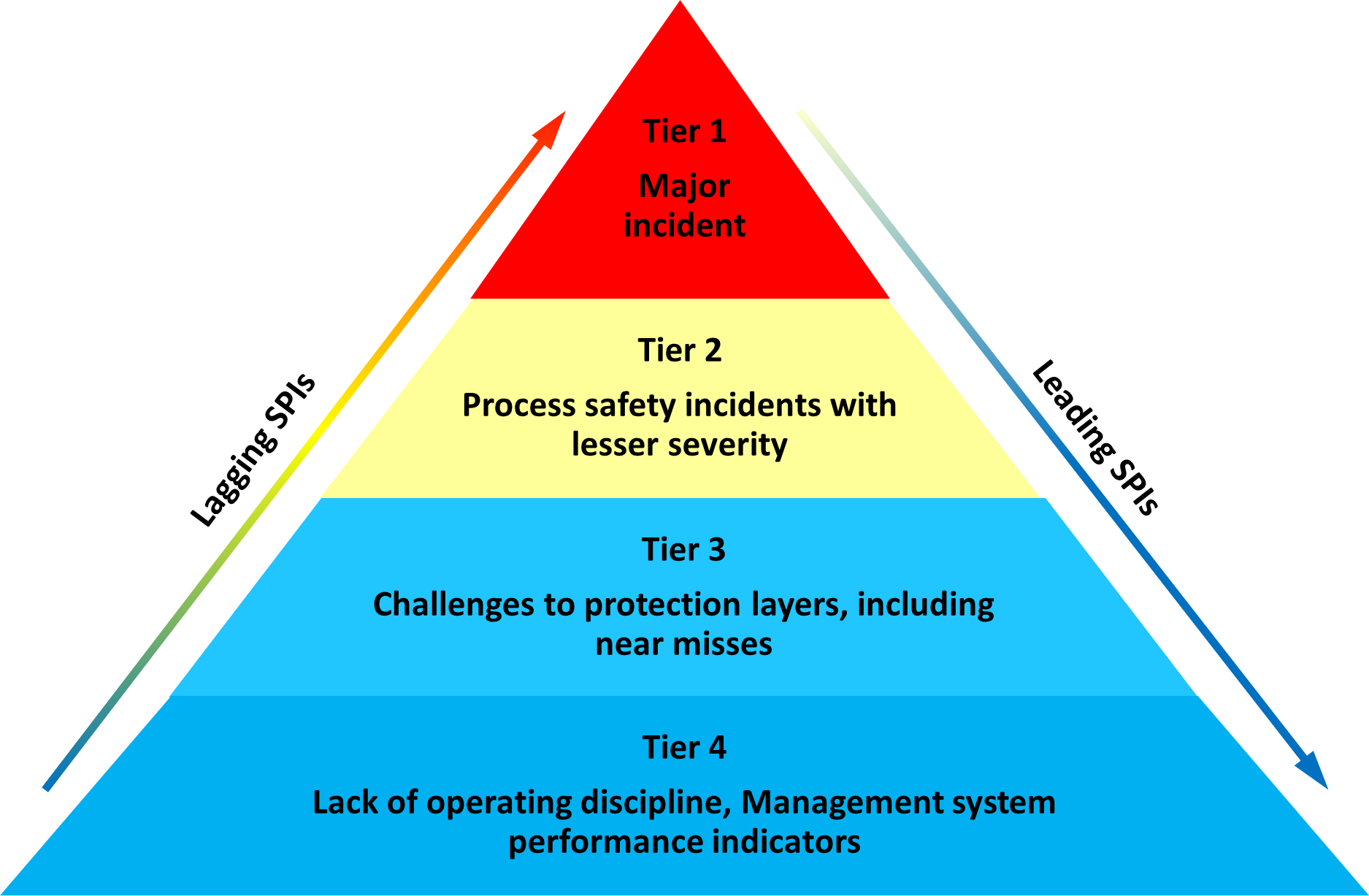
Figure 1: Tier-based approach to selecting SPIs [3]
Tier 4 includes proactive evaluations and continuous improvement efforts, such as operational discipline surveys, management reviews, process safety management system audits, and field observations. SPIs in this category are aimed to highlight a potentially elevated risk exposure relating to conditions and acts of commission or omission that increase the likelihood or consequences of a potential incident. There would also be an elevated risk exposure if there are significant gaps in risk control standards. Possible examples include:
- Diesel firewater pump extended outage – total reliance on electrically driven machines and therefore exposed to power failure during fire emergency.
- Management of change (MoC) process failed to specify operator training required before new system started up.
- Permit to work non-compliance: error on equipment number.
A near miss (Tier 3) is an incident with no actual consequence. However, if the circumstances were slightly different there could have been serious consequences. Examples include:
- Minor leak from hydrocarbon line due to incorrect gasket on pump discharge flange – able to switch to spare pump, isolate and fix the fault without a plant shutdown.
- High liquid level in flare knockout drum; level indicator faulty – but problem identified by operator visual checks before liquid carried over to flare stack.
- Defective construction weld on hydrocarbon lined is discovered by inspection at turnaround.
Some examples of a minor incident (Tier 2) include:
- Pump seal leak – hydrocarbon released but not ignited.
- Emergency shutdown of process unit due to heater tube failure
- Leak on hydrocarbon piping – weld failure due to construction defect.
- Flexible hose bursts on truck loading rack – manual emergency safety shutdown activated by operator
|
Some examples of a major incident (Tier 1) include:
- Vapor cloud explosion from hydrocarbon leak causing fatalities and major damage.
- Floating roof full surface fire taking several days to extinguish.
- Spill fire beneath vacuum tower causing collapse.
- Uncontrolled internal tube leak resulting in complete destruction of furnace.
|
5.2 The barrier approach
The barrier approach is based on the well-known “Swiss cheese model”, developed by James Reason, in which an organisation’s defences against failure are treated as barriers, and the failed barriers are represented by the holes in each slice of the Swiss cheese.[7]
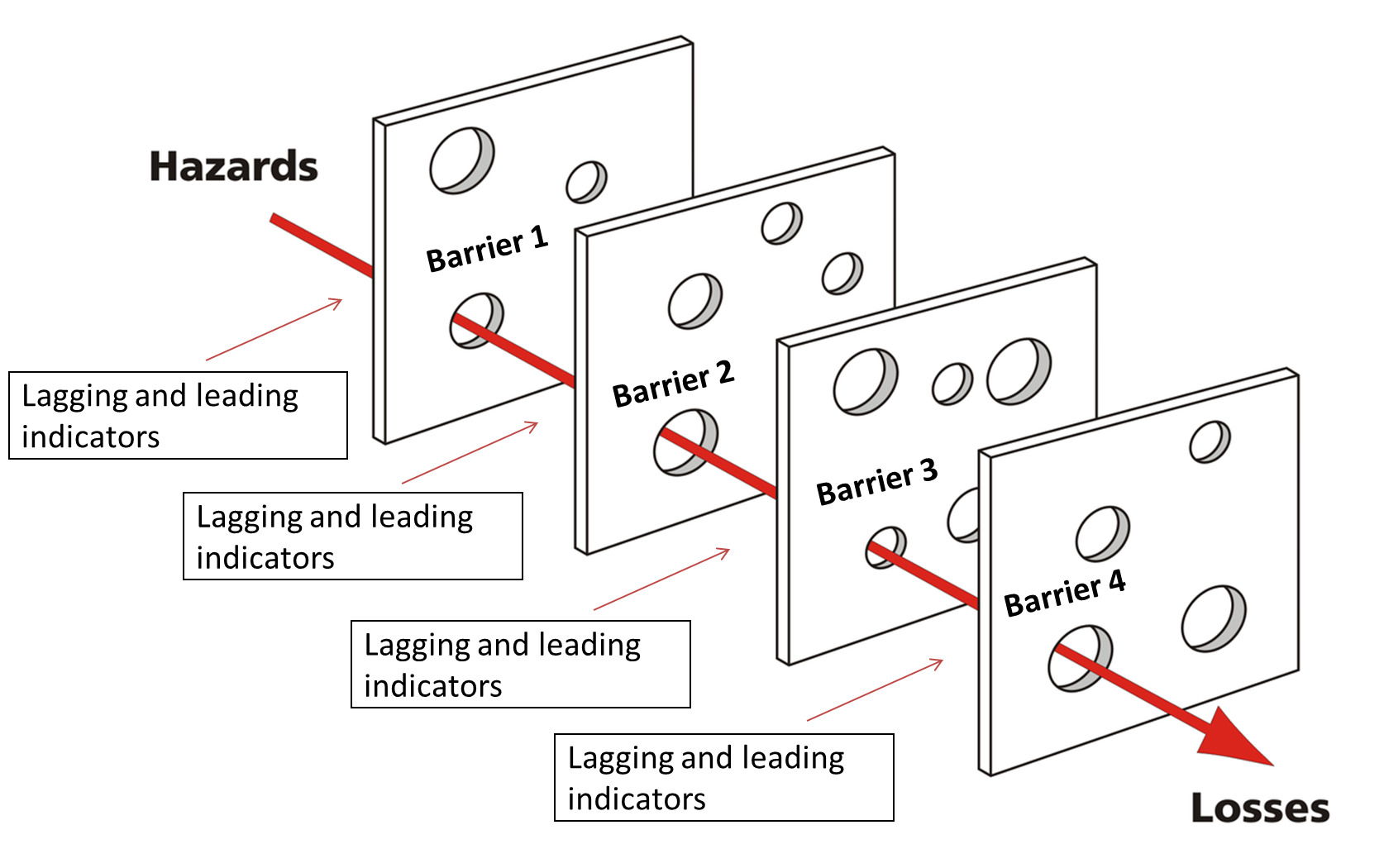
Figure 2: The Swiss Cheese model
Figure 2 illustrates leading and lagging indicators from the perspective of identifying potential weaknesses in barriers (leading indicators) or barriers that have failed (lagging indicators). The process safety performance should be designed to provide ongoing assurance that risks are being adequately controlled. Leading and lagging indicators should be established in a structured and systematic way for each critical risk control system within the whole process safety management system.
Plants may differ in terms of types of risk control systems that should be covered by the SPI programme. As examples, HSE lists plant change, inspections and maintenance, staff competence, operating procedures, emergency arrangements, and permit-to-work systems, but there can be many more. The IChemE Safety Centre (ISC) proposes one approach that barriers can be classified into six “functional elements”, which are engineering and design, knowledge and design, systems and procedures, monitoring and evaluation, human factors, and safety culture [11].
Elements |
Metrics |
|
|
|
- Deviations to safety critical elements (SCE)
- Short term deviation to SCE
- Open management of change on SCEs
- Demand on SCE
- Barriers failing on demand
|
|
- SCE Inspections Performed Versus Planned
- Barriers fail on test
- Damage to primary containment detected on test/inspection
- SCE maintenance deferrals (approved corrective maintenance deferrals following
- risk assessment)
- Temporary operating procedures (TOPs) open
- Permit to work checks performed to plan
- Permit to work non-conformance
- Number of process safety related emergency response drills to plan
|
|
- Number of process safety related audits to plan
- Number of nonconformances found in process safety audits
|
|
- Compliance with critical procedures by observation
- Critical alarms per operator hour
- Standing alarms
|
|
- Open process safety items
- Number of process safety interactions that occur
|
Table 1: ISC, 2015 Lead Process Safety Metrics [11]
Table 1 shows leading indicators called lead process safety metrics that ISC published for these categories. Figure 3 shows an alternative way to look at risk control systems.
There is also a distinction between those SPIs used at different organisational levels of a major hazards business, as illustrated in Figure 4 and is heavily influenced by the needs of the different end users. At the plant level there is a greater number of SPIs to control major hazards and as these are aggregated and rolled up to higher organisation levels there will necessarily be fewer SPIs.
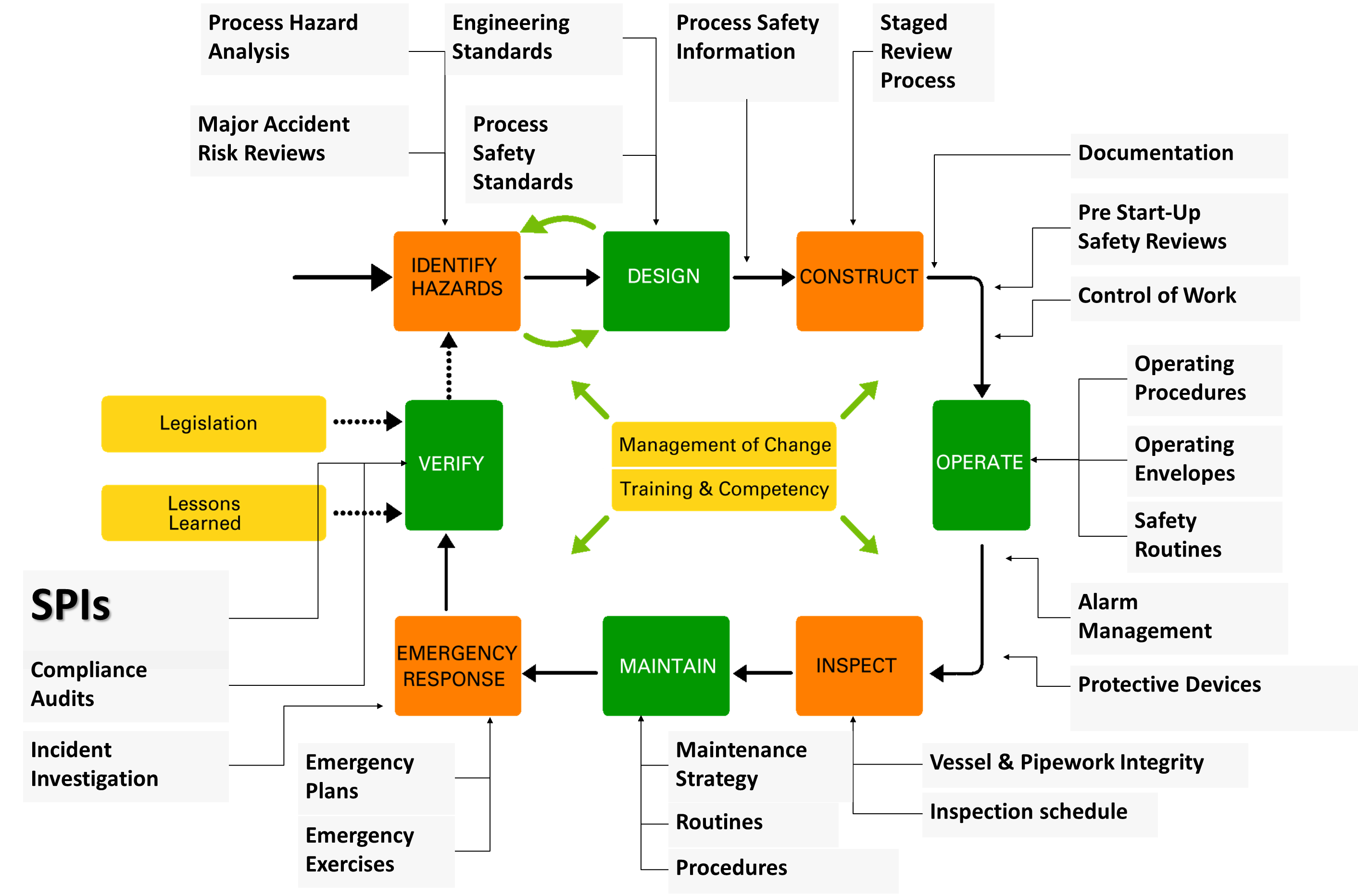
Figure 3: Schematic of typical risk control systems
6. Description of the SPIs process
SPI programmes can be considered to comprise four phases, that is: conception, design, operation, and evaluation. Generally, the greater the workforce engagement during each phase the more likely that SPIs will become a successful tool in managing process safety. Conversely minimal workforce engagement during the process is more likely to result in the programme being neglected or even abandoned.
6.1 Conception
The conception phase is about assigning roles and responsibilities and considering who needs to be involved, who is taking the lead, who is providing direction, whose buy-in is needed, and who needs to be consulted. Once this framework is in place, the implementation team can then identify the major accident barriers by interrogating the risk profile of the operation, understanding what can go seriously wrong and prioritising the areas for SPIs.
6.2 Design
The design phase is about the selection and definition of SPIs. This process requires identifying the risk controls in place for the major accident barriers and focusing on those that are both critical and vulnerable. Lagging SPIs should provide feedback on how well barriers are working. Leading SPIs then measure what needs to be accomplished in order to ensure success. Lagging and leading SPIs are developed in turn for the major accident barriers that have been identified in the conception phase.
As far as the SPIs themselves it is important that they are well grounded into the operation and meet the SMART requirements as below:
Sufficient |
- Enough data to drive improvement over the reporting period
|
Measurable |
- Data can be collected efficiently
|
Accurate |
- Workforce will accept the accuracy of the data
|
Reliable |
- Workforce buy into value of providing data
|
Targeted |
- Focused on incidents and weaknesses in risk controls
|
The following are examples of SPIs that typically meet the SMART criteria:
- Control of work - permit non-compliances (open/closed)
- Compliance audits - action items overdue
- Inspection schedule - overdue inspection recommendations
- Operating envelopes - operating window excursions
- Process hazard analysis- scheduled hazard reviews and completed and associated action items completed
- Emergency plans - crisis management exercises (actual versus target)
- Training and competency - staff safety critical competencies compliance
- Management of change – open MoCs & overdue temporary MoCs
Note that on different sites there may be equally good or better alternatives to measure the elements above. The selection will depend on what is relevant and practical for the site, and the characteristics of the risk control system.
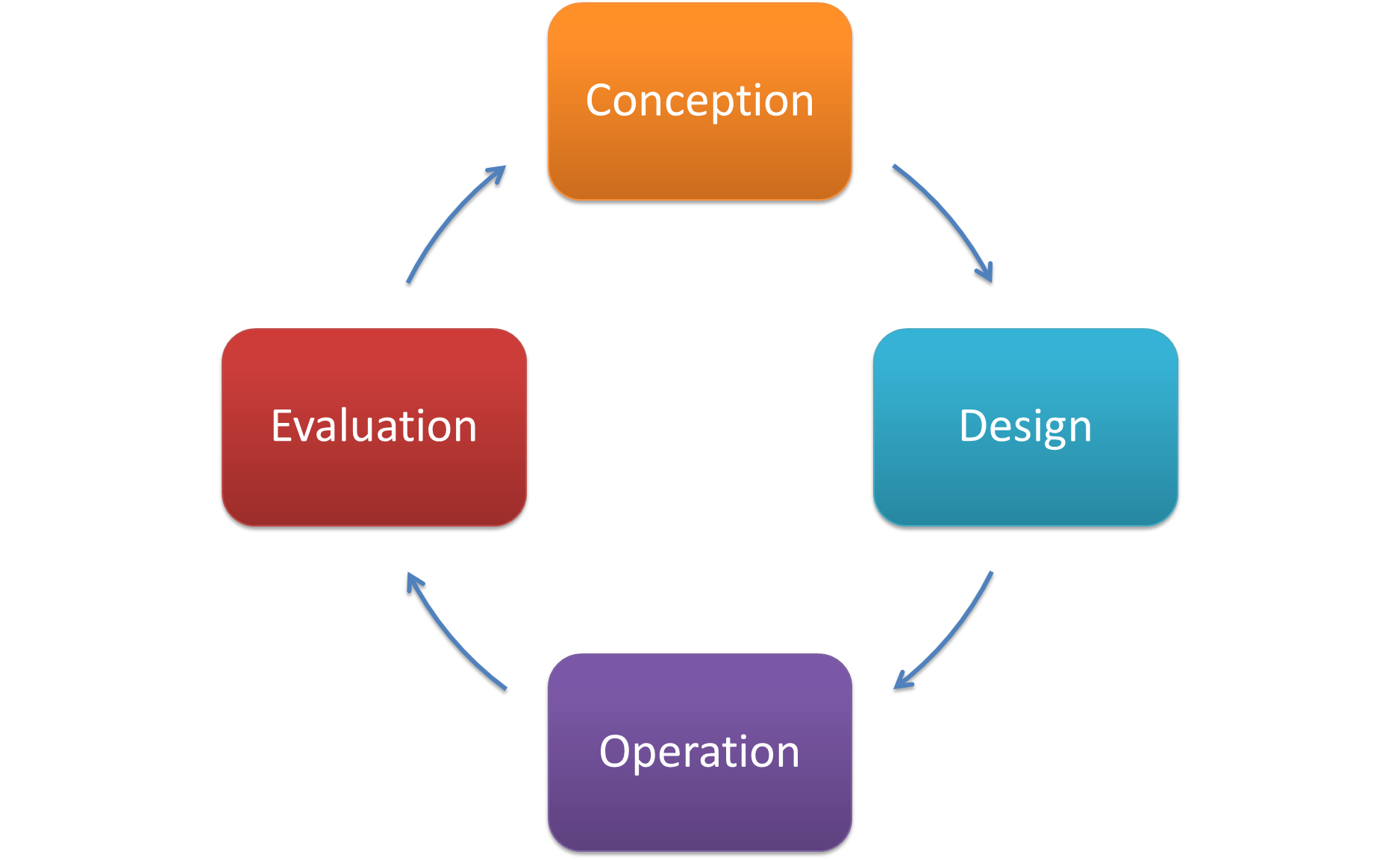
Figure 4: SPI Design Process
6.3 Operation
The operation phase concerns the collection and analysis of data which supports the defined SPIs. The frequency of collecting, analyzing, and reporting the data needs to match the rate at which the risk control might degrade, whilst providing a meaningful number of data points. The data analysis needs to be presented in a clear manner so that decisions for action can be taken. It is important to remember that SPIs only provide benefit if action is taken to make corrections or improvements.
6.4 Evaluation
Risk control systems tend to degrade over time. This can go unnoticed, particularly where degradation may not have an obvious impact on day-to day site operations. For example, failure to maintain a pressure relief valve on a vessel will probably not affect normal operation but could lead to catastrophic failure during a process upset. It is good practice to use SPIs to proactively detect weaknesses or failures within the critical systems. This enables remedial action to be taken before, rather than in the wake of, a major accident.
Operators should regularly assess and review how well they are managing their major risks. This can involve the targeted sampling and testing of risk control measures. Senior managers should regularly ask themselves as to whether they have a satisfactory grasp of the SPIs which are being reported upwards to them in making appropriate risk informed decisions.
Hence, at periodic intervals, the SPIs should be evaluated as to whether they are providing sufficient feedback on safety performance and that the targets of the measures are relevant for that purpose. This review may trigger a new cycle of conception, design, operation, and evaluation.
In this context, it is important to recognise that SPIs may have a finite life. When specific SPIs fail to add value then they should be retired especially as and when new indicators are introduced. Some operators will adopt a policy of “one SPI in, one SPI out” in order to keep the total number of SPIs to a manageable level. This number depends on the capacity and appetite of a business to both analyse and act on the SPIs and the value each is believed to add to the management of major hazards.
7. Techniques for evaluating SPIs
There are a number of ways to review SPIs to help understand whether the operator’s SPI programme is properly targeted and calibrated to generate accurate feedback on process safety performance. These strategic questions can be used equally by operators or inspectors to examine the effectiveness the effectiveness of the site’s SPI programme.
Where SPIs have not been established or where SPIs exist but are not effective then operators/inspectors should consider the following questions:
- Is this part of a wider issue? If there are no SPIs for several of the critical control areas and there are no other effective means of monitoring performance, this can indicate significant weaknesses in the safety management systems
- If SPIs are being monitored but findings are not acted upon, this suggests a preoccupation with analysis, “paralysis by analysis”, or simply organisational inertia
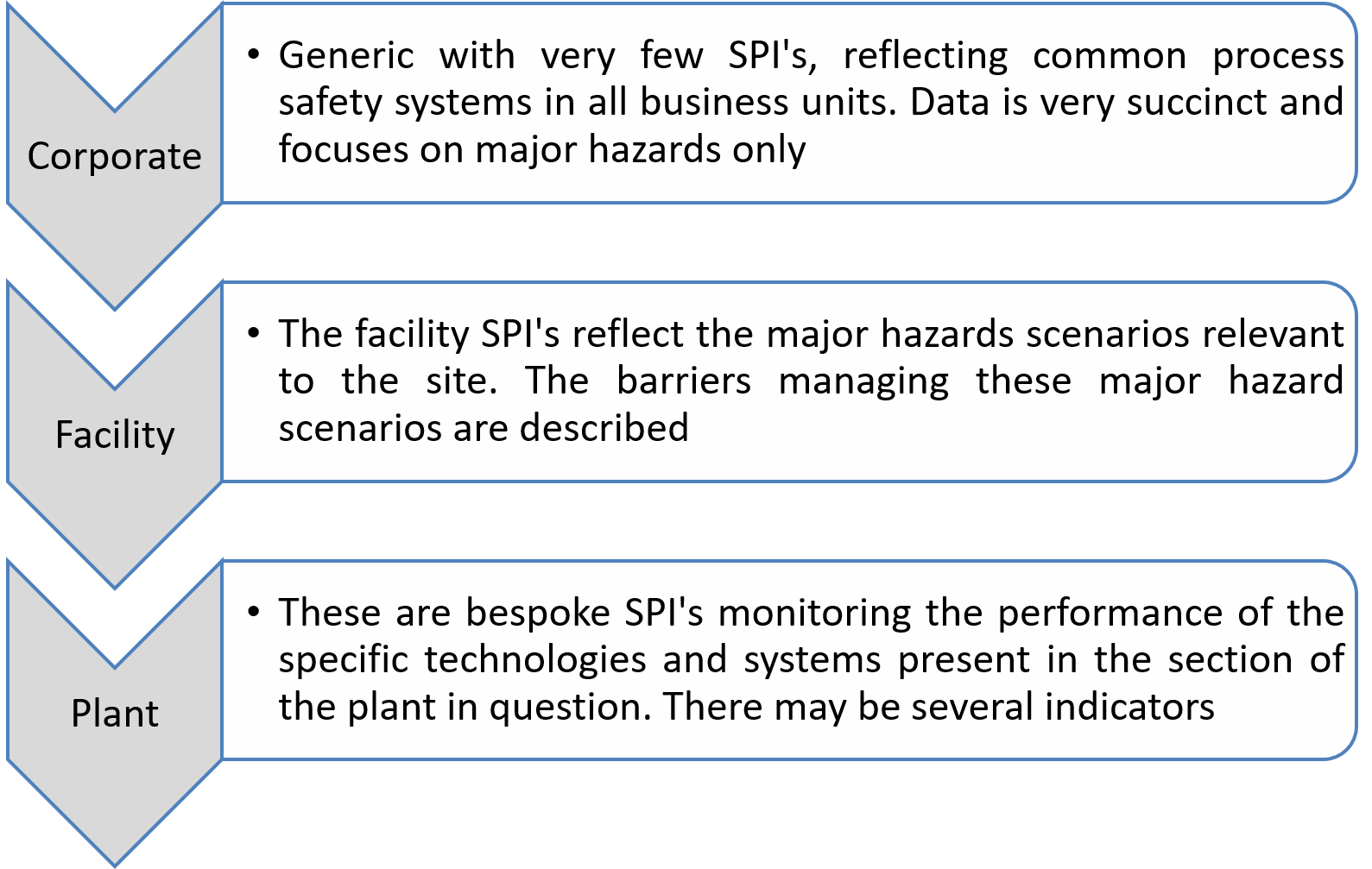
Figure 4: SPIs can be assigned to different levels of the organisation
7.1 Evaluating SPIs after process safety incidents
A process safety incident, be it of actual or potentially serious consequence, presents an opportunity for operators to investigate which key elements of risk control have failed, e.g., protective vs. mitigatory barriers. [10] Investigators/inspectors should establish whether SPIs were being used to monitor them. If so, they should check:
-
The usefulness of the information received, e.g., are they measuring the wrong things such parameters where there is a weak or tenuous link to a credible major accident scenario?
-
Was the indicator too far removed from the critical control, e.g., competence being measured by training courses attended rather than assessment of critical staff against clear competence criteria?
-
Was the indicator set against frequent enough events to give useful information?
-
Was the indicator tolerance appropriate, e.g., SPIs set against damaging excursions beyond design tolerance of the plant?
-
In cases where the SPI was appropriate, were safety decisions being made based on the information received?
7.2 Evaluating corporate leadership and the SPI program
-
Good leadership is essential for a successful SPI programme and senior managers should be regularly challenging themselves, and inspectors may also find it useful to challenge them, with the following questions [8]:
-
Do you rely mainly on personal accident and injury rates to monitor safety performance within your organisation?
-
Do you have specific SPIs for major hazard risks?
-
Were you involved in setting the SPIs for your organisation and do these measures reflect your understanding of the main process safety risks within your organisation?
-
Do you have a manageable number of SPIs or do you ‘over measure’ because you find it difficult to identify the main areas of vulnerability within your organisation?
-
Do you understand what the change in the status of each measure means for the control of risk?
-
Are you certain that the information SPIs provide leads directly to a change in the way you manage risk?
-
Do you always expect the status of the SPIs to be acceptable?
-
Does the culture of your organisation encourage upward reporting of bad news?
-
Do you regularly review the range of SPIs you have to ensure that they reflect the main vulnerable areas in your management of risk?
-
Do you benchmark your major hazard performance against other organisations in the same or similar sectors?
8. Communication of SPI results
The success that an organisation realises from its use of SPIs will be primarily determined by how effectively it communicates performance outcomes. It is important to actively and openly report, present and share these across all levels of the organisation. This includes everyone from the executives and senior management that make decisions about how resources will be allocated to line management, supervisors and workers who will be responsible for introducing and acting upon any operational change.
Many major hazard organisations use awards, incentives and recognition schemes to encourage interest amongst staff towards SPIs and improved management. Leading performance indicators are ideally suited for use in incentive schemes. The process for identifying suitable indicators helps to increase workforce engagement and develops ownership of the programme
Nevertheless, the award of payment bonuses can generate behaviours that can make them counterproductive. One main risk is that goals that are expressed in numerical terms lead often to ‘gaming the system’ such that the SPIs become a preoccupation instead of the risk areas they highlight. These can result in:
- non-reporting,
- adjusting estimates of releases to enter lower categories
- rescheduling actions to avoid overdues,
- using light duty to reduce the number of LTIs and
- sacrificing quality in favour of quantity.
|
It is therefore necessary for bonus systems to be carefully designed to guard against these counterproductive unintended consequences.
9. Types of safety performance indicators for different sectors and maturity levels
Typically, multinational companies and global players have SPIs that are established at a corporate level and mandated to be collected and reported upwards from site level. This top down approach has its advantages and can prove beneficial if information and outcomes flow both ways such that all workers are engaged in the SPI programme.
In addition, several trade bodies or group of companies who have similar operations have collaborated at a national and European level to produce a SPI template for their particular industry sector. (See References [1] [2] [3] [4] [5] [11]) This works well when there is little variability between the operations of the individual companies but would not be suitable for a varied industry such as specialty chemicals manufacturing.
Safety performance indicators may also be used in the public sector to monitor themselves in the performance of their role in reducing chemical accident risk. The OECD has produced guidance for developing SPIs for both industry as well as for public authorities and communities with responsibilities associated with protecting citizens and workers from chemical accidents.[13] [14] [14] Public authorities can also use SPIs to monitor industry, as highlighted by RIVM in its literature review of SPIs used in controlling major hazards, although it cautions that regulators must measures should be considered relevant by the industry and practical and valid across the range of sites subjected to the measures.[15]
A good example is the work completed by HSE in the UK explosives industry [9]. A template has been produced with SPIs defined for different stages of the supply chain and unit operations. The SPIs are designed to cover both leading and lagging indicators. They will not be appropriate for all operators, but it is intended that individual companies select those SPIs which are most useful for their particular operations. This means that individual companies spend less time in specifying which SPIs should be measured and can, instead, make use of the work completed by the expert group. As such, it is particularly useful for industries which contain a large number of companies employing relatively low numbers of people and where technical resources are limited.
SPI’s should not be regarded as a guaranteed solution to poor safety performance that will deliver instant results. For poor safety performers, where leaks and spills are accepted as the norm, it would be better for the operator to target first the obvious shortcomings and deficiencies, be they in the plant, the process or the people, and then establish an operating SMS to ensure that safe operation is reliable and consistent. Only then may the introduction of SPI’s add value.
References
- API, 2016, Recommended Practice (RP) 754, Process Safety Performance Indicators for the Refining and Petrochemical Industries, 2nd Edition http://www.api.org/oil-and-natural-gas/health-and-safety/process-safety/process-safety-standards/rp-754
- CEFIC, 2016, CEFIC Guidance for Reporting on the ICCA Globally Harmonised Process Safety Metric http://www.cefic.org/Industry-support/Responsible-Care-tools-SMEs/3-Plant--Process-Safety/Cefic-Guidance-on-Process-Safety-Indicators/
- Center for Chemical Process Safety (CCPS), 2011,Process Safety Leading and Lagging Metrics CCPS, New York, NY. https://www.aiche.org/sites/default/files/docs/pages/CCPS_ProcessSafety_Lagging_2011_2-24.pdf
- Center for Chemical Process Safety (CCPS) Information page on process safety metrics, including multiple language versions of its guidance on lagging and leading indicators, https://www.aiche.org/ccps/resources/tools/process-safety-metrics
- Energy Institute, Process Safety Management, https://www.energyinst.org/technical/PSM
Guidance on meeting expectations of EI process safety management framework https://www.energyinst.org/technical/PSM/psm-guidelines
- Hailwood, M., Safety Performance Indicators. Prepared for the EC-Austria Mutual Joint Visit Workshop. Hernstein, Austria, 10-12 April 2018.
https://minerva.jrc.ec.europa.eu/en/shorturl/minerva/mjv_austria_home_page
- Health and Safety Executive, 2006, Developing process safety indicators - A step-by-step guide for chemical and major hazard industries ISBN 978 0 7176 6180 0 http://www.hse.gov.uk/pUbns/priced/hsg254.pdf
- Health and Safety Executive (HSE), 2008, Key Process Safety Performance Indicators - A short guide for Directors and CEOs http://www.hse.gov.uk/leadership/keyindicators.pdf
- Health and Safety Executive (HSE) (2008) RR909 - Safety performance indicators in the explosives sector: Development of a worked example http://www.hse.gov.uk/research/rrhtm/rr909.htm
- Health and Safety Executive (HSE). HID Instruction: Assessment of Key Performance Indicators During Inspection/Investigation http://www.hse.gov.uk/comah/hid-kpi-delivery-guide.pdf
- ICheme Safety Centre (ISC), 2015, Lead Process Safety Metrics – selecting, tracking and learning, https://www.icheme.org/media/1092/safety-centre-metrics.pdf
- Jennings, K., Hailwood M. (2009) OECD Guidance on Safety Performance Indicators – An International Approach to Assessing the Success of Industry, Public Authorities and Communities in Managing Major Accident Hazards, IChemE Symposium Series No. 155, Hazards XXI https://www.icheme.org/~/media/Documents/Subject%20Groups/Safety_Loss_Prevention/Hazards%20Archive/XXI/XXI-Paper-030.pdf
- OECD, 2008, Guidance on Developing Safety Performance Indicators for Industry 2nd Edition, ISBN: 9789264221741 (PDF) http://dx.doi.org/10.1787/9789264221741-en
- OECD, 2008, Guidance on Developing Safety Performance Indicators for Public Authorities and Communities/Public 2nd Edition, ISBN: 9789264221734 (PDF) http://dx.doi.org/10.1787/9789264221734-en
- RIVM (National Institute for Public Health and the Environment, the Netherlands), 2012, A literature review on safety performance indicators supporting the control of major hazards, RIVM Report 620089001/2012 L.J. Bellamy | V.M. Sol, http://www.rivm.nl/bibliotheek/rapporten/620089001.pdf
PDF Version for printing
Process Safety Performance Indicators
Go back to the Common Inspection Criteria website
Now available: Handbook of Scenarios for Assessing Chemical Accident Risks
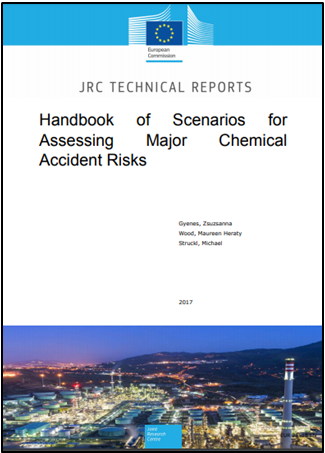
This report presents the collective work of the European Working Group on Land-Use Planning and discusses the activities towards more consistent land-use planning decisions through more understandable risk assessment approaches and data. The purpose of this book is to assist the EU Member States, especially those which do not have a consolidated system of approach, scenarios and criteria to assess the Land-Use Planning cases, in complying with the requirements of the Seveso Directive.
All JRC-MAHB publications can be found at https://minerva.jrc.ec.europa.eu/en/shorturl/minerva/publications