Link to .pdf
Link to Seveso Inspection Series Home Page
MJV Good Practice Report
Liquefied Petroleum Gas (LPG) and Liquefied Natural Gas (LNG) Sites
This short report is offered as a tool for use in Seveso inspections on LPG and LNG sites. It highlights important issues and suggests questions that could be incorporated into the inspection plan for a particular site, for pre-planning or during inspections on site. It also gives guidance on developing, testing and reviewing onsite and offsite emergency plans. It suggests trends in the LNG and LPG industries that will affect the sites and their associated risks in the future. Reflecting the views and experiences of MJV participants, various types of LPG and LNG sites that are not Seveso sites but do appear to represent major risks are also discussed.
Natural gas and petroleum gas are the principal fossil-fuel gases that arise from oil and gas production. They are primarily natural gas (predominantly methane with some ethane), propane, and butane. They can be stored and used under pressure in the gas phase. However, in many cases the gas will be liquefied and may be refrigerated to increase mass and energy density, for ease of storage and transport. This report focuses on these gases in liquid form. Their use is very widespread. As environmental and climate-change policies change, these gases are replacing many other fossil fuels, because they are relatively “clean-burning” fuels.
LNG and LPG sites are included in the Seveso Annex 1 Part 2 [1] defined named dangerous substance “Liquefied flammable gases”, together with other gases. Lower tier classification is 50 tonnes and upper tier, 250 tonnes. The hazards and risks associated with these sites are driven fundamentally by the physical and chemical properties of the substances, and their storage conditions. The main hazards derive from their flammability, such that they can result in fire and explosion, leading to catastrophic escalation including vessel rupture (BLEVE).
1European Economic Area (EEA) countries are Iceland and Norway
To discuss these particular hazards, the Cyprus Department of Labour Inspection and the European Commission’s Joint Research Centre (JRC) hosted a Mutual Joint Visit (MJV) workshop on LPG and LNG sites for Seveso Inspectors from 26-28 September in Nicosia, Cyprus. The purpose of the workshop was to share lessons learned and good practice for risk management and inspection of LPG/LNG sites within Seveso countries. The workshop also recorded various concerns of different states about some developments and trends. This short report is intended to provide concise and early guidance for Competent Authorities (CAs) and their front-line inspectors, about significant issues, trends and information that arose at the MJV Workshop.
This Seveso Inspection Series good practice report is a summary of a Seveso Inspection Series expert report of the same name. The full report can be found under Publications at: https:// minerva.jrc.ec.europa.eu
Seveso sites associated with LPG and LNG in Member States and EEA countries vary between none and many hundreds. There are many more LPG Seveso sites than LNG. Although it is not possible to identify exactly how many Seveso sites are associated with LPG and LNG, many countries have identified LNG and LPG storage sites within the EU’s eSPIRS Seveso database.
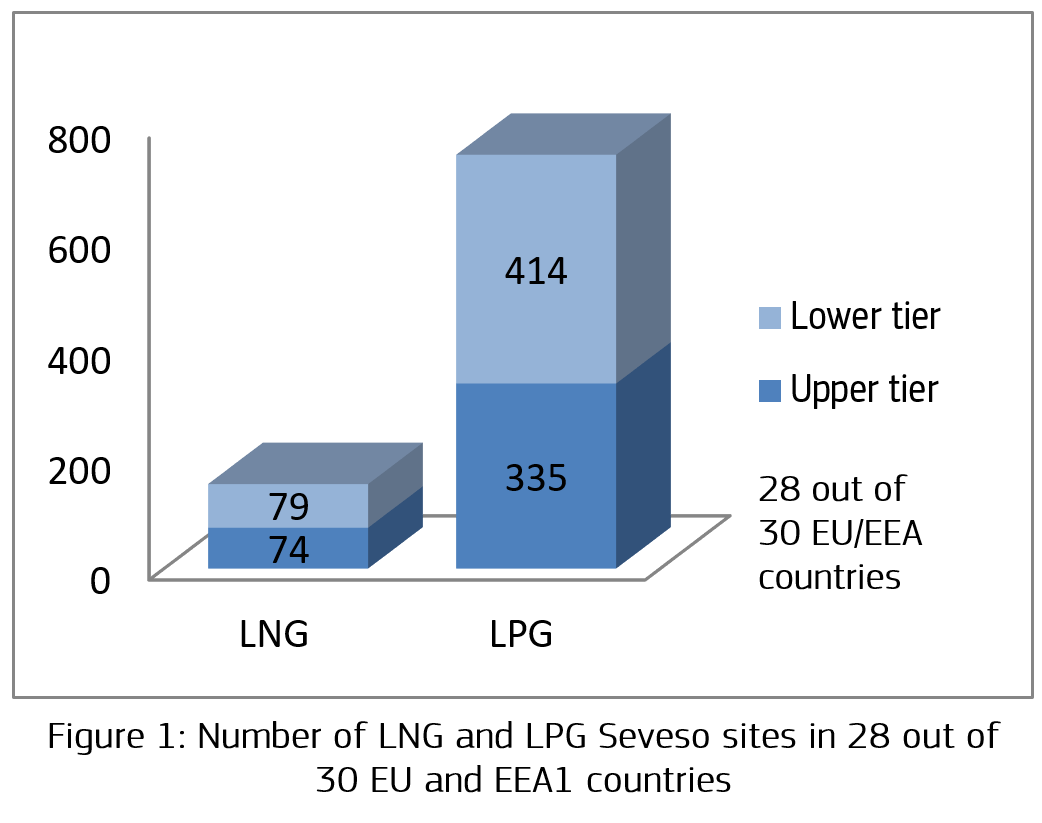
As shown in Figure 1 above, there are well over 700 LPG Seveso sites and more than 150 LNG sites in EU and EEA countries. The number of sites per country varies considerably, from less than 5 to many hundreds. Moreover, workshop data from 16 countries indicate an additional 11,000+ LPG sites and nearly 200 LNG sites in these countries that are not covered by the Seveso Directive.
The age profile of sites also varied greatly. States who had large numbers of sites tended to have older sites, reflecting a gradual build-up of such sites over time. For some states, both LPG and LNG are commonplace. In others, one or other may exist and inspectorates may have little or no experience of the technology and risks when new sites are proposed or developed.
The full detailed record of the MJV can be found on the EC Europa website: https://minerva.jrc.ec.europa.eu/en/shorturl/technical_working_group_2_seveso_inspections/mjv_lpg_and_lng [2]
2Society of International Gas Tanker and Terminal Operators
-
1 Liquefied Petroleum Gas (LPG)
The manufacture, import storage bottling and transport for pressurised LPG is a long established industry in those countries and regions where there is no or limited natural gas distribution network. Its use as a road fuel has grown significantly. It may be pure propane, pure butane or sold as mixture in gas
Figure 2 below shows the potential range of sites, containment and means of transport. It will commence with production from a refinery or a gas reception terminal which may already be an upper tier Seveso site, import by pipeline or ship, either pressurised or refrigerated. LPG marine tankers tend to be smaller than LNG tankers to facilitate regional distribution to smaller, more remote communities. Both the ships and the terminals they visit should comply with SIGTTO2 guidelines but these do not require the more sophisticated arrangements that are found on the large new LNG tankers and terminals. All these sources would feed bulk storage which may be refrigerated at atmospheric pressure (- 43oC for Propane and -3oC for Butane) or stored in spheres or bullets at the ambient temperature with pressure ranges from 4.0 – 13.0 bar for propane and 0.0 to 2.8 bar dependent upon the ambient temperature. It may then be distributed by road, rail or pipeline to depots for further local distribution or retailed as a mixture of both propane and butane in gas bottles (cylinders) or disposable canisters with vapour pressures in between these figures. These smaller depots and filling stations may fall below the Seveso lower tier threshold.
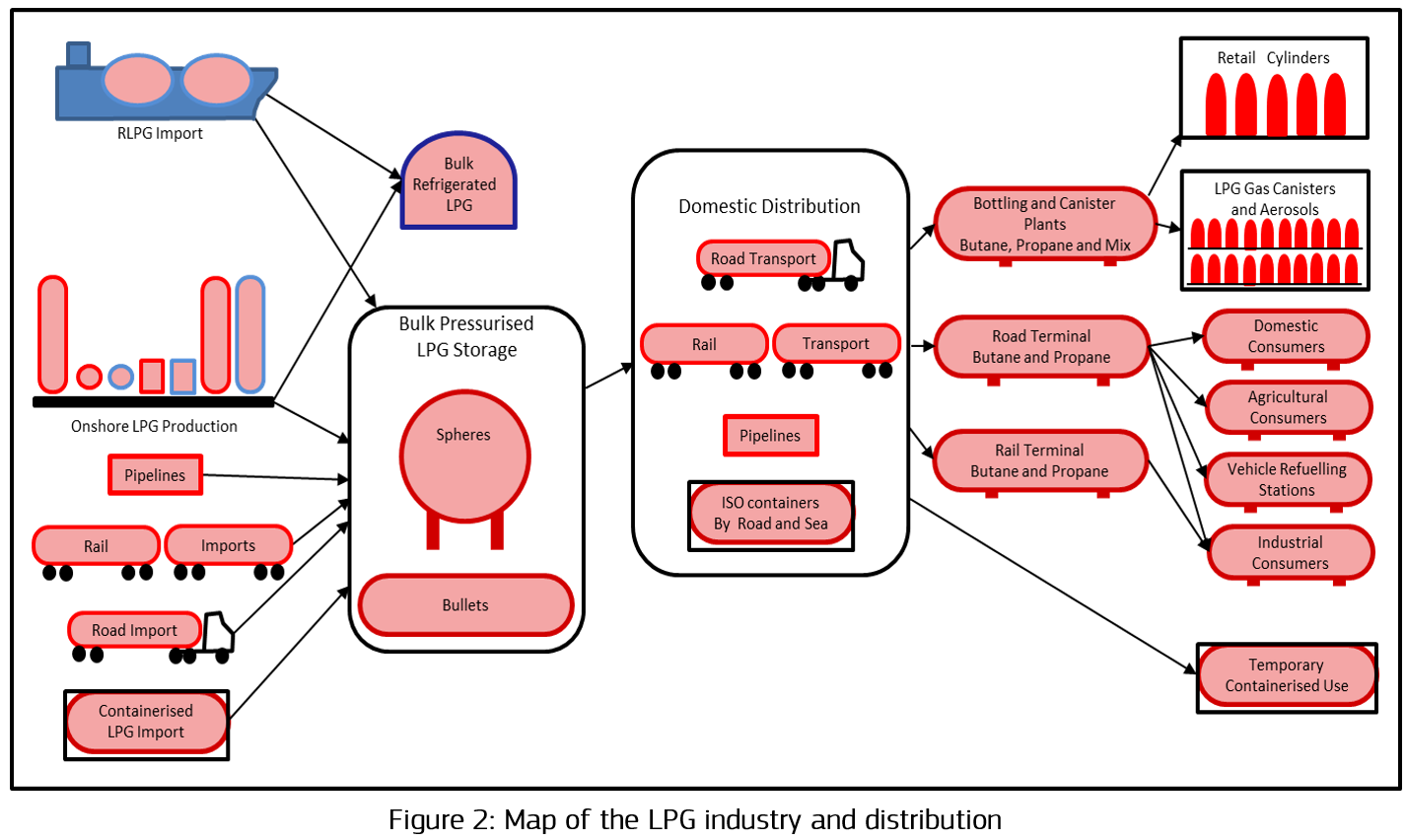
There is also a growing use in import and distribution in pressurised ISO containers. This may be more difficult to monitor and regulate. The diverse and mature nature of the industry means that there will be a series of different parties owning the plant, the LPG and having responsibility for safe operation, transfer and transport. The OECD studies into ownership change of chemical plants resultant guidance [3] showed that the LPG site distribution industry was particularly prone to such changes, particularly the end of the line distribution and retail industry.
The hazard effects are well understood, with flash fires and explosion risks arising from the heavier than air gas potentially spreading into congested, enclosed and occupied spaces with rapid flame front velocities giving high overpressures with possible catastrophic detonation, as well as jet fires from pressurised LPG. Both liquid and gas phases have very high heat fluxes leading to the rapid heating and catastrophic rupture (BLEVE) of bulk pressurised containment. Very large scale accidents occurred at Feyzin in France in 1966 [4] and San Juanico in Mexico City in 1984 [5]. Many smaller scale incidents involved rail cars, e. g., Lillestrøm in Norway in 2000 [6], Viareggio in Italy in 2009 [7], and also in bottling plants, e.g., Bedale in England in 1995 [8]. Despite the understanding of the risks, emergency response personnel continue to put themselves at risk attempting to cool plant to prevent escalation and many have died as a result. The risks from canister and aerosol filling may have been overlooked but could result in rapid sequential rupture of thousands of containers within minutes causing both immediate personnel consequences and possibly unanticipated widespread effects beyond the site boundary.
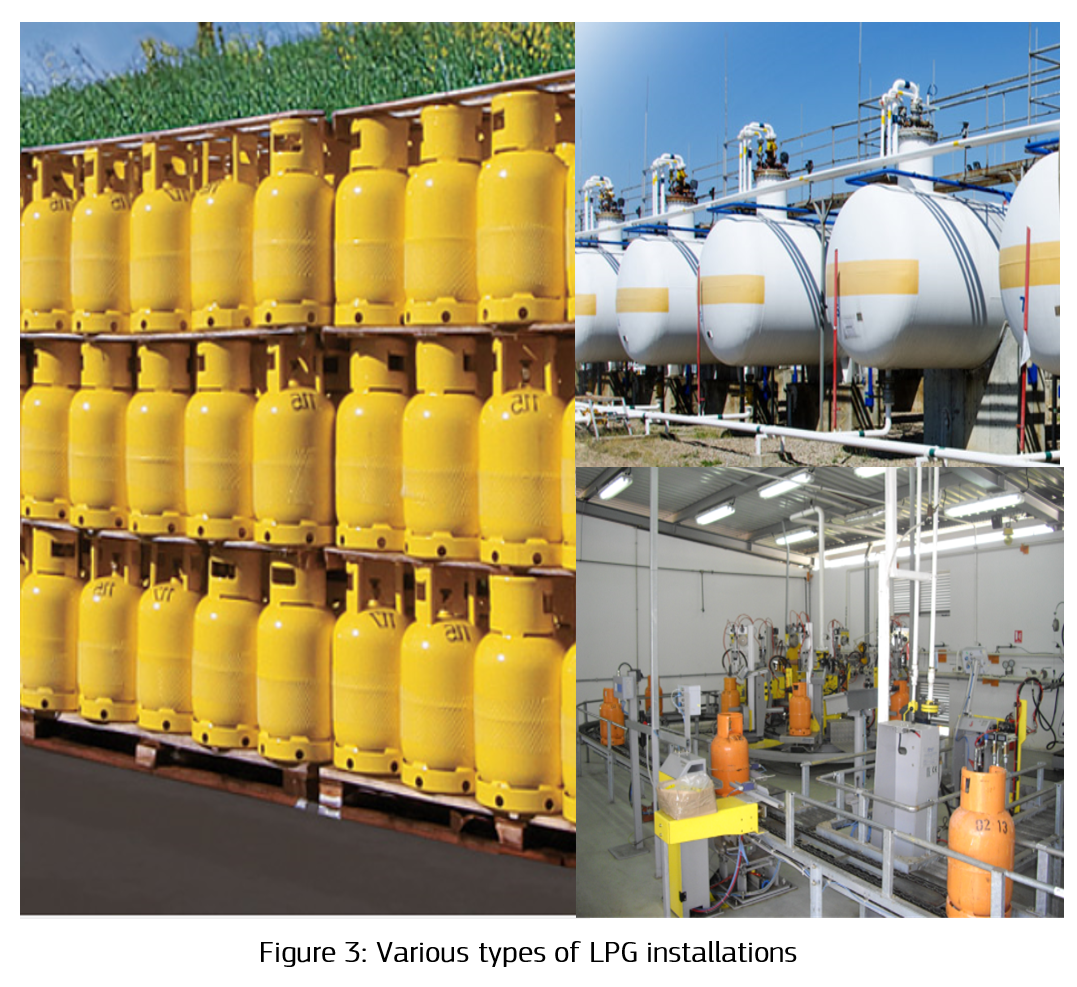
-
2 Liquefied Natural Gas (LNG)
LNG has been used commercially since the mid-1960s. For the greater part of that time, LNG has mainly been used as a part of the bulk transport of LNG by ship in gas carriers over large distances, in the absence of suitable natural gas pipelines. There has been a marked increase in the production of LNG with the development of gas reserves in remote locations and the augmentation of the supply for large consumers especially Europe driven by the vulnerability and depletion of their existing sources. Gas reserves in the northern North Sea and Mediterranean may be developed for export. The refrigerated LNG at gas field terminals is the start point for the production and supply of LNG as shown in Figure 4. LNG cannot be transported by pipeline. It will almost always be located on a coastal site, either as a reception, processing or export terminal for gas reservoirs or as an import terminal. It will be liquefied by refrigeration (to -160oC) and stored in insulated double walled bulk tanks at or near atmospheric pressure, and then transferred to gas carriers. This will be referred to as RLPG for this report.
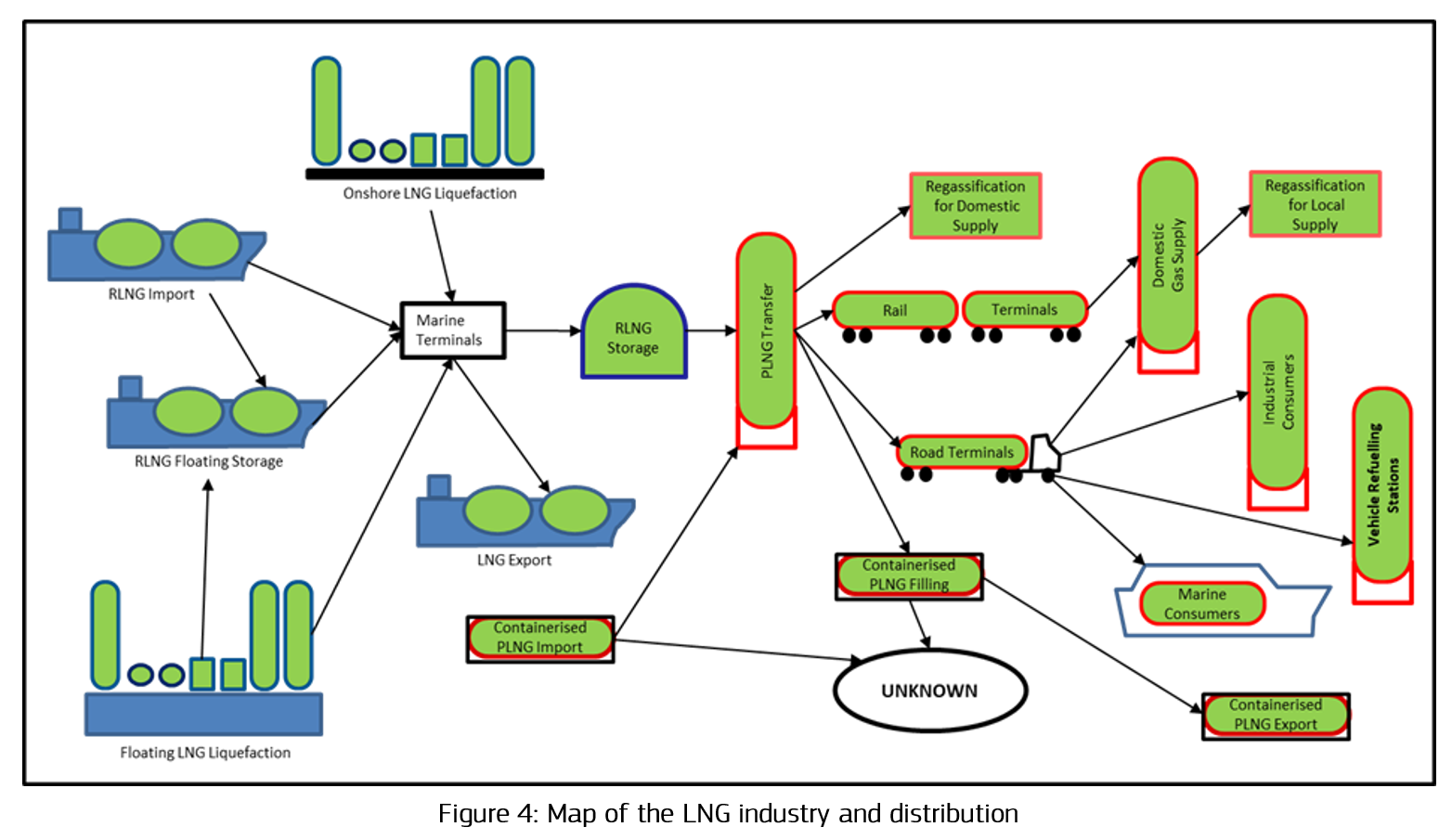
The import marine terminal is essentially the reverse of the export: reception of LNG from berthed gas carriers, with bulk refrigerated LNG storage and either subsequent vaporisation to the gas phase, for use or transmission down a pressurised gas pipeline, or further distribution in smaller insulated semi pressurised tanks. These are insulated containers, initially filled at minus 160oC which may progressively rise up to minus 110oC and 10 bar and are referred to as PLNG, i. e., pressurised LNG in this report. It may be transported in specifically designed road and rail tankers. It is also being shipped in ISO containers which may also be moved by sea providing another means of national import. This is a relatively new and developing field and its development and additional hazards specifically discussed in 2.2. In another incident, explosives stored in shipping containers exploded when subject to a very high ambient temperature. This was a case where the civil storage facility was unaware of the nature of the contents of the containers
The main hazard of LNG is associated with its flammability (whether as a flash fire, pool fire, jet flame or even possibly an explosion). However, LNG’s properties suggest that the flammability hazards are inherently less than those for LPG with lower flame velocities, overpressures and heat fluxes. The large inventories and the potential for catastrophic failure of the containment have given rise to concerns about very large heavier than air cold gas clouds spreading over large distances before heating sufficiently to warm up and disperse. The LNG industry has performed many LNG release trials to determine how it will and disperse but these are highly dependent upon the initial event, the spill containment and the energy available to vaporise the liquid. The assumptions regarding any event modelling should be clearly explained and critically reviewed in the Safety Report.
One issue with LNG is that it is impractical to add an odoriser to it in liquid form. This means people may not notice a small leak or appreciate the spread of a large one and their exposure. This puts a greater dependence upon fixed gas detection which should be located and designed to identify a cryogenic gas cloud. There is also uncertainty about the flash fire and UVCE risk in open spaces such as harbours. A recent review by the UK HSE [9] suggests caution before entirely discounting UVCE for LNG. However, the increasing industrial and marine use of PLNG may lead to its location and refilling close to buildings and occupied areas where there could be a risk of a confined or congested explosion.
The escalation risk with LNG may be lower than for LPG with robust RLNG storage in double and full containment tanks and minimal pressure containment to lead to violent rupture. It cannot be entirely discounted as a viable event for PLNG tanks or RLPG plant and piping as both can sustain relatively high pressure although the insulation may reduce the risk.
The cryogenic effects of the liquid LNG pose a risk both of loss of containment and the effects on plant, structures and people in the vicinity of any release. If the equipment has not been designed to cope with cryogenic temperatures, it may be vulnerable to brittle fracture. Although not an LNG site, one well known example of this is the Esso Longford accident in Australia [10]. Cryogenic liquid gas arrived in a section of the plant not intended to contain such cryogenic fluids. It failed through brittle fracture, leading to a major accident. Early in the history of LNG shipping, small LNG releases at the loading-arm connection between gas carriers and marine terminals lead to fractures of unprotected hull plate. This was subsequently designed out by extending the catch-trays under the load arms to contain the LNG spill to cryogenic compatible areas. Personnel in the immediate vicinity of a cryogenic release have died delaying warnings and immediate response. Structures supporting critical plant, instrumentation, monitoring and shutdown systems may also fail.
-
2.1 Refrigerated LNG (RLNG) Sites
The growth in LNG Import has led to public concern about the scale of hazard and risk perceived to be associated with storage and transport of “vast” quantities of “highly flammable” gases, and typically this is still raised when new RLNG installations are proposed. Despite over 50 years of experience or shipping and storage of RLNG, only a few major accidents have occurred, and most of those were in the industry’s early years. This is no doubt due to the generally high standards that the industry has developed and implemented, as prescribed in the SIGTTO presentation and codes of practice [13], NFPA 59A [11], EN 1473 [12] and all its subordinate and connected European standards. There is still some uncertainty about the real likelihood of a catastrophic release, given the good operational historical record and relatively limited data and operational experience, particularly in Europe, concerning the likelihood of more serious events. Flat bottomed tanks would be designed to be one of the following, each with a pressure rating of around 0.5 bar.
- · Single Containment where only the inner shell is designed to contain the liquid with a non-pressure rated outer shell for the insulation and a bund or dike to prevent uncontrolled spillage.
- · Double Containment where both the inner and outer shell are designed to contain the liquid but only the inner shell can contain the vapour. The outer shell will be less than 6m from the primary containment and is usually concrete .
- · Full Containment as double containment except that the outer shell and roof can contain the vapours in the event that the primary containment fails.
A discussion on the relative risks is given in [14].
Storage tanks may be subject to Rollover. This effect arises because natural gas is not a single component fuel but a mixture of methane, ethane and other hydrocarbons depending upon the source. Storage and transportation can result in weathering where the lighter components preferentially vaporise further increasing the proportion of heavier components and the density. This can also cause stratification within a tank with the lower density LNG below the higher density. It can cause a rapid release of LNG vapour as a result of the spontaneous and turbulent mixing of stratified layers of different densities of LNG in a storage or cargo tank, particularly when filling a partially filled tank. SIGTTO have published detailed guidance on the phenomenon, how it occurs and how to manage it [15]. There are 2 main aspects to the management of rollover. Firstly, the storage needs to be designed to both cope with rollover by providing adequate relief system capacity (to avoid failure of LNG containment), and also provide filling arrangements to allow stratification to be avoided in operations. Such relief venting of LNG (methane) is undesirable but a lesser event than wholesale loss of bulk LNG containment, and a far larger LNG release. The second issue is that operational measures should be in place to identify circumstances likely to give rise to stratification of stored LNG, and operate the plant to avoid it. Examples include the storage of LNG from different sources, the weathering of an LNG parcel or the creation of nitrogen-induced stratification.
The interface between the LNG carrier and the terminal is the other major risk source with the loading arms and connection being a potential source of large bore release and catastrophic failure of the hull or terrorist attack potentially leading to loss of the tank integrity. SIGTTO, the society of gas tanker and terminal operators have been instrumental in producing and implementing high standards and good practice for all aspects of design and operation. Compliance with their standards gives reassurance that these risks are being managed effectively [13].
In the event that there is a catastrophic release of LNG onto the sea surface or a large volume of liquid such as a bund, Rapid Phase Transition can occur. In the presence of a significant source of heat, almost always water, the LNG rapidly changes phase from liquid to vapour. RPT has also occurred when LNG has leaked into drip trays under ship manifolds This requires a large amount of energy to be taken up from the water but does not involve the ignition and burning of the natural gas: a “cold” explosion. The hazardous effects are the blast wave from the explosion that can propagate either in the air or water. Experience of accidental effects is fairly limited but it is speculated but not proven that, for example, an LNG release onto the sea could cause significant damage to the underwater hull of a gas carrier. Avoiding releases is perhaps the most obvious risk reduction measure. In addition, keeping water out of areas that might receive accidental LNG releases will avoid RPT making the release event worse. Examples are the drip trays under cargo manifolds and bunded areas around single containment tanks.
-
2.2 Floating Refrigeration and Storage of LNG
Recent trends in the LNG industry are leading to very large integrated floating processing, refrigeration and storage barges and to the use of LNG carriers as permanently moored storage facilities. These may be moored several miles offshore if there is a benign or sheltered environment or to a purpose built jetty. They may receive and dispatch RLNG cargoes either with loading arms and arrangements to the SIGTTO standards [13] or may use simpler ship to ship connections which may not benefit from as effective safeguards. They may export RLNG or PLNG to shore or else vaporise it for transmission into the national gas network.
The Seveso Directive is not clear on the classification of these facilities and whether they come within the Directive. It may be a national decision how to address their regulation and enforcement, whether it comes under marine and transport of dangerous goods or under Seveso. There may be additional aspects to any risk assessment and management such as the ship to floating facility interface, and the interface with land based storage and processing. The facilities are likely to be designed and built outside the country in which they are to be located and this may require processes that assure that the design and construction have been carried out to minimise the risks of release and a major accident.
-
2.3 Partly Pressurised LNG (PLNG)
The MJV identified the established use of partly pressurised LNG, PLNG for industrial and marine use in the Scandinavian countries. It is also being actively marketed in other parts of the EU, particularly the UK. It uses the technology already established for other liquefied gasses, oxygen for hospitals and liquefied nitrogen of cryogenic use and refrigeration with its storage in double skin vacuum insulated tanks at pressures of up to 10 bar and temperatures of up to minus 110oC. The liquid is vaporised in heat exchangers as required both for consumption and for maintaining the tank pressure. A typical facility is shown in the picture below.
The increased demand is partially due to the environmental aspiration to reduce the carbon footprint. Worldwide, probably the most significant change is in the general shipping industry, where the IMO (International Maritime Organisation) is moving to phase out heavy sulphurous fuel oils, with initial proposals to phase them out in in the Arctic by 2020 [16]. LNG appears to be the favoured option and it is already in use in ferries in Norway and refueling has started in the UK and other countries. This is likely to lead to a very significant increase in demand in ports and the need either for a permanent storage facility or supply by road or rail with direct refueling from tankers or ISO containers. Although without the Seveso remit, very useful guidance is given in the IMO IGF code on the Safety for Ships using gases and other low flashpoint fuels [17].
Its use is increasing in industry and remote communities where PLNG can be transported to regions which have no domestic piped gas supply. It would appear that this growth could be outpacing the development of effective regulation, guidance and industry codes of practice, particularly in countries where it is being introduced for the first time. This is particularly relevant to the understanding of the hazard effects which would be essential for effective site risk assessment and default recommendations for siting and separation distances.
At present, the industrial use is being promoted by the major LNG operators in each country. They would appear to offer a complete service of design, siting, supply of the facilities and delivery of the PLNG but the day to day responsibility for safe operation will lie with the user. The LNG is usually delivered by road tanker and transferred under pressure to vertical tanks in the case of industrial use or to dedicated tanks on ships and ferries. Typically industrial sites have a large single tank which would be sited to have both road access and reasonably proximity to the consumers. An example is shown in Figure 5.
![Figure 5: A typical PLNG gas supply for an industrial facility (C. Sandqvist, MJV Workshop [2])](/en/shorturl/minerva/f5png)
As with LPG, the siting, ownership and responsibility for the PLNG storage may not reside with the factory owners, rather with the gas supplier or an intermediary distribution company. They would also be responsible for the filling, inspection and servicing of the facilities with that generally being carried out through single man operation, the driver of the delivery truck. However, the site management will be responsible for the day to day operation, the control of activity and emergency response. Unlike LPG, PLNG relies upon insulation, usually a vacuum, to limit the heat input and boiloff. Without it or consumption of the gas, the pressure would rise above 10 bar with the excess vented to atmosphere. This requires procedural controls both by the user and the delivery driver to control the pressure and temperature of the tanker and storage tanks. If left for several weeks without drawoff, it will eventually require relieving the pressure and venting the gas to the atmosphere.
The growth in its use for industry does not appear to have been matched by the understanding of the specific hazard effects and this appears to undermine the reliability of risk assessments. At present, the effects of pressurised cryogenic liquid releases, typically 10 bar and -110oC are less well understood than those for atmospheric RLNG. The pressure will give greater release rates and spray formation which may result in a jet fire or 100% vaporisation of an unignited release and a bigger gas cloud, or there may be liquid drop out and pool formation. Another uncertainty is the behaviour of the storage tanks when damaged or exposed to fire. Loss of the outer vacuum containment will give higher heat input and vaporisation. In a fire this may cause much greater heat input but the contribution of the double skin and the insulation if present may significantly reduce the possibility of rupture, i.e., BLEVE but it may not eliminate it. Gas composition and impurities such as the proportion of ethane and other heavier gases increases the risks in RLPG and may affect PLNG too.
The lack of an odoriser may increase the risks to local personnel through delayed warnings if there is no gas detection. This uncertainty about the hazard knowledge was reflected in the MJV and may hinder effective risk assessment.
While much of this will not come within the Seveso Directive because of the size of the storage, it may still constitute a significant major accident risk with the contributory factors of ownership and responsibility, sites with no experience of major accident or flammables management, single man working, and the proximity to a manned industrial site or the public. On the positive side, LNG is relatively pure, non-corrosive, transferred under its own self-sustaining pressure, i.e. no pumps, and has limited potential for a major gas release and cloud formation from the vapour part of the operation. This leaves the prevention of liquid releases as the primary risk control measure. These sites will almost certainly have a relationship with a bulk storage refrigerated LNG storage facility through the supply and transport of the PLNG and it may be advantageous to use a common inspection and regulation authority.
![Figure 6: LNG floating storage unit (G. Papadakis, MJV Workshop [2])](/en/shorturl/minerva/f6png)
Some of the risk drivers are common to both the LNG and LNG industries but others are more specific due the relative age and maturity of the two industries.
3.1 Ownership, accountability and responsibility
The nature of both sectors is such that the primary bulk supply of both LNG and LPG will come from large well established companies who are competent in the management of major accident hazards. They will probably provide part or all of the national supply and the sites are likely to be upper tier Seveso sites. This will be a certainty where the LPG and LNG is refrigerated or spheres are used for LPG. They will own the liquefied gas, the plant, and either directly employ the workforce or have effective control over contractors. They should have comprehensive operating and integrity management systems with competent personnel and control of work which can be verified as part of the Safety Report and follow up inspections. As the LPG and LNG pass along the distribution chain, through pipelines, rail and road transport, the ownership both of plant and contents and the responsibility for safe operation may become less clear. This becomes critical once ISO containers are used. The distribution depots and bottling plants are likely to be Seveso sites and many will be lower tier. The distribution and use of PLNG as shown in Figure 4 (on page 4) is still relatively new and these sites are likely to be owned and managed by the source company but this may change. In the LPG industry, these may be SMEs and be separate from the support and infrastructure of major chemical companies. Integrity management such as vessel inspection and testing may be contracted out and limited to pressure systems. One explosion on an industrial consumer’s site resulted from failings during the pressure testing of the storage bullet.
Much of the MJV focused on the distribution and final use of the LPG and LNG. While this may fall outside the Seveso notification, it is likely that the depot and distribution companies will be responsible for the siting, filling and integrity of the end users plant, particularly for PLNG. The engineers and managers setting up the client’s industrial site and the delivery drivers will be the primary points of contact. Through these relationships, there is an opportunity to influence those end user risks even though they are unlikely to be Seveso sites.
3.2 Quantities, site layout. location and storage arrangements
The potential for harm is a function of the quantities, storage pressures, the number and arrangement of the storage of cylinders and the proximity to people. The largest quantities by far will be the atmospheric refrigerated storage tanks. Modern arrangements would normally be double walled cylindrical tanks with the outer wall capable of containing the entire inventory in the event of inner tank failure but older LPG tanks may be single skin with limited containment by the bunds or dykes in the event of catastrophic tank failure as occurred in Umm Said in Qatar in 1977 [18]. Large scale pressurised LPG storage would be in Horton spheres containing 100 – 6000 tonnes or in arrays of bullets each containing several hundred tonnes. There is potential for escalation with either type of storage resulting from fire engulfment or explosions, particularly from the heavier LPG if it spreads into congested or enclosed areas or offsite. Catastrophic escalation is a primary concern with pressurised LPG storage where there are a number of storage vessels with domino escalation and rupture as in Mexico City or fail due to loss of structural support. The most recent practice for pressurised LPG sites is to mound bullets but this is not universal and has not necessarily been applied retrospectively.
The construction, age and inspection of the tanks will dictate the likelihood of failure. The age of some LPG vessels and RLPG tanks means that they may have been constructed to older standards, that their inspection and testing has been overlooked if the site has changed hands and that they may be corroded, particularly on coastal sites. Corrosion under insulation on a refrigerated LPG plant almost resulted in a catastrophic release in the UK. In other cases, operation of seawater based deluge systems caused corrosion under the cementitious passive protection on the legs of a Horton sphere.
The layout of the site and the adherence to defined vehicle routes, parking, loading, laydown and storage areas contribute to minimising the likelihood and escalation of an initial incident. This is particularly important in cylinder filling and distribution depots where the uncontrolled movement and laydown of cylinders has caused accidents involving fork lift trucks with the subsequent sequential rupture of the cylinders travelling offsite and endangering of the bulk storage. The spread of a gas cloud through a series of banks of cylinders could lead to highly turbulent flame fronts and high explosion overpressures, possibly up to detonation requiring precise definition of the locations, arrangement and maximum numbers of cylinders that can be stored on site. The storage of gas canisters and aerosols should be examined as there may be thousands within warehouses and a small fire could escalate very rapidly with the almost simultaneous rupture of the entire inventory.
Gas detection is a key requirement in the absence of an odoriser in LNG to facilitate early warning and initiate Emergency Shutdown. With effective tank integrity and protection from fire, the potential for loss of their contents is governed by the speed, effectiveness, and protection from harm of the ESD valves. Failure to maintain and test, or reliance on manual intervention, magnifies the risk from a downstream release.
3.3 ISO containers
The increasing use of ISO containers both for LPG and PLNG is of concern. It will not be clear who owns the containers and the liquefied gas within it, how they are tracked, shipped, stored, inspected and where the contents are used. There appears to be no limitation on the numbers of containers which may be stored together. They will fall outside the Seveso directive and possibly outside national LPG and LNG regulations. It is possible that quantities far in excess of the Seveso lower threshold could be stored at container ports, or on trains. It is also feasible that LNG import in ISO containers is the first way in which LNG would be introduced to a country which has not used it before and that it will become a primary means of PLNG supply for ships. It requires vacuum insulated pressurised tanks.
The ownership of the tanks and contents and the responsibility for them while in transit or storage may be an area of uncertainty both for the ports and the regulators. A filled PLNG ISO container may take days and possibly weeks before there is sufficient heat ingress to cause the relief systems to vent, but it will eventually do so, with the discharge at pressures around 10 bar and temperatures of -110oC. In most cases, the rate of release may not be sufficient to offer a significant risk if ignition or fire loading but, conversely, it may not be noticed due to the lack of an odoriser or detection. Damage to the outer vacuum shell or heat from another source could lead to much higher heat input giving greater relief rates and the relief valves may not be sized for that heat input. ISO containers are likely to be stacked and the frames are unlikely to be passively protected. A fire would lead to their rapid weakening and toppling of the whole stack with possibly catastrophic vessel failure. Emergency response is also likely to be hindered by the container port layout.
3.4 Operational procedures and practices
The existence and use of good practice for design, operation, and integrity management will depend upon the type and attitude of the duty holder. It should be well established in RLNG sites with the use of SIGTTO guidelines in marine terminals. Good practice may not have kept pace with some of the new developments such as the use of floating liquefaction and storage close to shore or at jetties. It has been difficult to find established national, corporate or accepted industry practices about the storage, siting, filling and operation of PLNG facilities. When these become available, they should mirror those which are established for LPG.
Careful operational controls are needed for the safe transfer of both LPG and LNG to prevent overfilling, rollover and overpressurisation. These need to be augmented by accurate metering both on trucks and plant, level indication, and weight sensors. The age, ownership, and competition of the LPG distribution industry could undermine the use and compliance with good operational practices. Complacency is a threat and there is considerable evidence of single person working, particularly where drivers are responsible for loading and delivering the gas. Their competence and compliance with effective procedures is critical both on the Seveso loading depots and at the customers. The use of trucks with integral transfer pumps further compounds this situation requiring the truck engine to keep running during transfer with no means of shutoff and isolation other than the driver who may be incapacitated by the initial incident [M. Goethals, MJV Workshop [2]]. In the case of LNG, there is also the possibility that a lone operator could be incapacitated by the cold and asphyxiation. At least one fatality has been attributed to the release of cold PLNG at a vehicle refuelling station in the US.
LPG bottling plants will depend on manual processes and handling with semi-automated filling lines, manual handling, and fork lift trucks. Canister and aerosol filling is likely to be fully automated. The storage arrangements, locations and limits for the numbers of LPG cylinders and canisters should be clearly defined as these are a source of release, increase congestion which could increase potential explosion overpressures and would rupture in a short time when engulfed in fire.
4 Inspection strategy
The national inspection strategy will need an overview of the whole picture of LNG and LPG as outlined in Figures 2 (page 2) and 4 (page 4).
4.1 LPG Inspection
LPG is likely to be a long established and diverse industry with a number of companies sharing responsibility for production, importation, transport, bottling and distribution with blurred responsibilities. Older plant built to earlier standards may not include modern detection process control and shutdown systems. It may have changed hands, and have deteriorated with limited inspection and certification. Change of ownership or complacency may have undermined to safety culture and the implementation of effective safety management. A first step would be to identify all of the players in the industry and those that cooperate or work within Seveso sites and to develop a strategy which will examine all of those who have direct or indirect responsibility.
4.2 LNG inspection
Conversely, LNG is a developing and evolving industry. It may already be established with the building of RLNG import terminals or liquefaction plant if there are large offshore natural gas fields. Most large marine terminals will be relatively new and those that are older should have an established track record. The use of pressurised LNG for industrial and marine use and for local domestic supply has become established in a few countries and is being actively marketed in others. In the early days, it is likely to be managed and operated by the primary LNG importers and producers but this is not necessarily the case, particularly if it is imported in ISO containers. It would be prudent to develop a good relationship with the main companies to identify how and where the industry is growing, who is involved and to ensure that the latest standards and knowledge are being applied for bulk storage transfer and use on site.
-
4.3 Sites operating without the Seveso Directive
The strategy should identify not only the primary Seveso sites but the ownership and responsibility of the plant, gas and transport. It should identify the interfaces with other regulations and regulators and those sites which have major LNG and LPG hazards operating without the Seveso III Directive. The MJV participants identified a number of such sites handling bulk LNG and LPG facilities and operations that posed a major accident threat. As many of the participants have responsibility for these activities, their experience and concerns are shared here. Some operators consciously size plant or arrange transport and storage such that either the sites are either below the Seveso tier thresholds. In some cases, the fixed storage, for example at industrial LNG or LPG consumers, is below the lower tier Seveso threshold but the total quantities on site exceed it when the road tankers are connected for topping up, a time of the greatest hazard. The specific concerns about PLNG are discussed in that section. The hazard effects could be the same as for Seveso sites with large heavy vapour clouds spreading away from the source with the potential for flash fire and explosion. However, the consequences could be more severe as the lack of Seveso permissioning and oversight may allow siting of the facilities such that the gas cloud could spread into occupied buildings and factories which would have ignition sources and the confinement which could result in catastrophic fatal explosions.
The following were identified as requiring a realistic siting risk assessment and effective regulatory oversight:
- · LNG and LPG bulk storage and use for industrial and local domestic use
- · Bunkering of ships and ferries with LNG
- · The use of rail sidings to store bulk LNG and LPG in railcars
- · Transport and storage of ISO containers of LNG, particularly the storage of multiple tanks in container ports
The use of ISO containers has the potential for uncontrolled import movement and use of both LPG and LNG. It may not be brought to the attention of inspectors. It would be prudent to alert national regulators covering the transport of hazardous goods and non-Seveso LPG/LNG sites so that the pattern of use can be identified and property regulated.
Sets of checklist questions are given here for each.
LPG Site Inspection Questions
- What national regulations cover LPG sites, including those without Seveso and do you liaise with their inspectors?
- Who owns the site and who has overall responsibility for the plant and operations?
- Does the site have support in the management of hazards from a corporate industrial organisation or is it an SME without specialist backup?
- What codes of practice and industrial guidelines does the site follow and base its management systems upon?
- Does the site layout separate the bulk storage from vehicle movements, long and short term parking, cylinder storage and filling plants?
- What industrial and residential property is within range of portable cylinders and bullets if they rupture in a fire?
- Have all pressure systems been inspected and tested and how has this been carried out with mounded bullets?
- What is the design of any RLPG tanks, their age, condition, and inspection history and do they have full secondary containment around the shell?
- Have structures and pressure systems which are underground, insulated or covered in passive protection been examined for external corrosion, particularly coastal depots?
- How is the vacuum on double skin PLNG tanks monitored and is the external skin routinely inspected for damage?
- Can the relief system on vacuum insulated PLNG tanks relieve the vessel if the vacuum is lost?
- Are there procedures for emptying LNG tanks or making them safe if there is a refrigeration or insulation failure?
- Where flexible hoses are used for LPG transfer, who is responsible for their condition, integrity and testing and are they satisfactory?
- Are there designated storage areas for full and returned cylinders, as well as limits on the numbers, and does the site comply?
- Is there effective access control and monitoring of all personnel and activity on site, particularly if contractors, customers, and suppliers work on site?
- Is the site clean and well-ordered with close control and monitoring of all activities and movements on site?
- What is the minimum manning for the site and for any hazardous operations such as road tanker filling?
- Are all road tankers used for supply and/or distribution owned and operated by the site and if not, what duties do the drivers carry out on site and what are the arrangements for assuring their competence?
- Are there processes for inspection and recertification of returned cylinders
- The gas is heavier that air and will not disperse easily. Where is it likely to spread and accumulate taking into account the topography and local wind conditions?
- Are the gas detectors and process sensors that will raise alarms and isolate the release from the main inventories?
LNG Site Inspection Questions
- What is the current scale and pattern of use of LNG and how is it likely to develop in the future, particularly PLNG?
- Who are the main companies and do they control or have responsibility for all aspects from import/production to consumers?
- Where other companies are responsible for the distribution and consumers facilities, do they have broad experience in major hazards and LNG and what international and corporate standards do they use?
- Are they aware of the hazards and hazard effects of LNG such as the gas dispersion and cryogenic effects on people?
- What planning and layout guidance is used regarding the siting of PLNG consumer’s tanks and does this give adequate separation from occupied areas?
- What systems and procedures do they work to and how is the competence of critical personnel such as tanker drivers assured?
- Are all pressure systems and hoses suitable for cryogenic temperatures?
- How is the composition of the LNG (ethane content) monitored and are the operators aware of any hazards, such as rollover or rapid evolution of gas that could lead to overpressurisation or release?
- Is there pressure relief for all piping systems? What could be isolated and how are unrelieved systems and hoses purged before use?
- What standards are used for the construction and insulation of PLNG tanks, ISO containers, and road tankers?
- How is the vacuum on double skin PLNG tanks monitored and is the external skin routinely inspected for damage?
- Can the relief system on vacuum insulated PLNG tanks relieve the vessel if the vacuum is lost?
- Are there procedures for emptying LNG tanks or making them safe if there is a refrigeration or insulation failure?
5 Emergency response planning
Good emergency response can only be based on a good understanding of the type, characteristics, scale, timing, and potential for harm of the events that are reasonably foreseeable. In major emergencies, the external emergency services will become involved, whether or not external emergency plans are required by the Seveso Directive. Prior communication of technical information about hazard effects, including site familiarisation visits is essential. Selection of appropriate emergency scenarios is a key input to generating and exercising realistic and effective emergency response plans. There is a balance to be struck between those events that are more likely and those that are more serious. In the end a judgment needs to be made, bearing in mind the details of the site installation and the results of risk assessments of the installation. Both the site and external ER plans should be based upon the hazards and their effects specific to the site in the safety reports. These can be judged against the general hazard effects for LPG/LNG, as appropriate. It is critical that the potential for catastrophic escalation such as BLEVE is identified and communicated including the circumstances under which it could occur. If there is doubt about the quality of information from the operator, it could be checked against other consequence assessments. The EU JRC provides both consequence and event tree examples for LPG and LNG [19].
Any ER to control and mitigate the event is entirely dependent upon notification and briefing by site personnel. These general issues are even more challenging for ER on “unmanned” or “low-manned” sites. Given that this is how part of the LPG and LNG industries are developing in some states, this was a major concern of the MJV participants about all aspects of ER response for such sites. The increasing dependence upon single man working and their vulnerability to the initial incident is a major weakness in ER for these smaller sites. This will also have a direct effect on the time when the alarm is raised and in turn the response time of the emergency services, the risks to them and their effectiveness.
Three types of event should be considered:
1. A large scale unignited gas leak extending beyond the site boundary
2. A smaller event, fire, or gas leak with the potential for explosion which has the potential to escalate to a catastrophic event
3. A catastrophic event which has occurred or is ongoing
In the first case, detection and the isolation of the source of the leak from the primary storage or marine inventories is paramount, together with the prevention of ignition. This would be difficult to manage if the gas spreads to domestic housing but roads, other industrial sites and harbours should be considered. This will require close cooperation between the site personnel and the external emergency services including the coastguard for coastal sites.
In the second case, detection followed by a combination of the inherent strength of the plant, fire protection, both passive and active, and the isolation of the primary sources is critical. Typically mounding of bullets, fully inspected passive fire protection, and automatic shutdown and isolation systems are key to controlling these events. This is primarily the duty of site personnel but external services may be called to assist once the operation of safety systems has been confirmed.
In the third case, the ER should focus on preserving the lives of those beyond the site boundary, limiting access and managing evacuation.
Questions for Emergency Response Planning and Capability
- Are the ER plans based on credible and well assessed events?
- Have all relevant external ER services been consulted in preparation of the off-site plans including fire, police, medical and, for coastal sites, the coastguard?
- How do site and external ER services liaise during the incident so that they remain informed and updated and can assess the situation?
- How are adjacent industry and local inhabitants warned about a gas leak and what is their advised response?
- Is effective ER jeopardised because of low site manning?
- Who has site responsibility for ER on industrial LNG/PLNG sites, ports, and container depots?
- Do the ER plans cover unignited, smaller and catastrophic events? Has the potential for catastrophic escalation and its timing been considered in the planning?
- Has the rapid failure of gas cylinders, canisters and aerosols been appreciated in the plans?
- Do internal and external ER teams carry out a dynamic risk assessment and discouraging futile hazardous intervention?
- Is there effective passive protection, mounding or double containment on the main storage?
- Are there means to assess the operation and effectiveness of critical control and ESD systems?
- Are there arrangements to make the plant safe and secure or dispose of any remaining hazardous inventory?
5.1. Off-site emergency response
There are 2 main strands to the off-site issues. Close prior liaison with public emergency services (ES) will be essential. Previously agreed effective communications between the operator and the public ES will be critical. Appropriate means of raising the alarm will need to be carefully agreed between the operator and the public ES. In the absence of site staff, the public ES will need to have much more detailed knowledge of the site and its safety systems, as well as information from the safety report (if any). All of this will need to be provided ahead of any emergency, as there will certainly not be enough time to provide it once an emergency has occurred.
5.2. Risks to emergency response personnel
A primary lesson from many LPG incidents is the risk to firefighters. Many have died in futile attempts to prevent the catastrophic rupture of pressure vessels or been exposed to explosions while attempting to control gas leaks. These personnel should only be deployed following a dynamic risk assessment if they have a clear objective and it is safe and practical for them to achieve it. It will also depend upon confirmation that active systems such as deluge and ESD have worked and the duration of the event before ER teams are mobilised. The full effects and potential range of catastrophic vessel rupture, sequential canister rupture in warehouses and confined or congested explosions should be appreciated by all those responding.
5.3. Critical detection, control and mitigation systems
In the absence of sufficient personnel to ensure that alarms are raised, emergency systems activated and external ER personnel are briefed, there will be greater dependence upon the following engineered systems. However, these will only be effective for the particular circumstances for which they have been designed. Their role and effectiveness should be verified during site inspections. It should be practical for both the site and external ER incident controllers to access this information and the status of critical systems during and incident, for example, in a safe control room or at the main gate. Typical systems that may be used include the following:
- · General Site Surveillance (CCTV of the site and immediate vicinity, boundary security)
· Detection Systems (Process alarms, fire and gas detection)
· Control Systems (Emergency shutdown, process and storage tank isolation)
· Bunding and Spill Containment and Disposal Arrangements (Outer RLNG/RLPG concrete tank shells, bunds, dikes, vaporisation/burn-off pits)
· Passive Protection Systems (Mounding over bullets, passive protection of structural supports and vessels, blast resistant control rooms, ESD valve boxes)
· Active Protection Systems (Fire pumps, deluge systems)
References
- 1. Seveso III Directive. 2012/18/EU.
- https://eur-lex.europa.eu/legal-content/en/ALL/?uri=CELEX%3A32012L0018
2. European Commission Joint Research Centre. 2017. Mutual Joint Workshop for Seveso Inspectors on Liquefied Petroleum Gas and Liquefied Natural Gas.
- https://minerva.jrc.ec.europa.eu/en/shorturl/technical_working_group_2_seveso_inspections/mjv_lpg_and_lng
3. Organisation for Economic Cooperation and Development (OECD). 2018. Guidance on Change of Ownership in Hazardous Facilities. Environment, Health and Safety, Environment Directorate.
- http://www.oecd.org/chemicalsafety/chemical-accidents/oecd-guidance-on-change-of-ownership-in-hazardous-facilities.pdf
4. UK Health and Safety Executive. 2010. COMAH Guidance Case Studies. Feyzin, France 1966
- http://www.hse.gov.uk/comah/sragtech/casefeyzin66.htm
5. UK Health and Safety Executive. 2010. COMAH Guidance Case Studies. Feyzin, France, 1966 Juanico, Mexico City, Mexico, 1984. http://www.hse.gov.uk/comah/sragtech/casepemex84.htm
6. Lillestrøm Norway 2000– Ragnhild’s presentation
7. Wikipedia. Viareggio train derailment.
- https://en.wikipedia.org/wiki/Viareggio_train_derailment
8. BBC 999 Series. Gas bottling plant fire Bedale.
- https://www.youtube.com/watch?v=Cpjb-0lGiyw
9. UK HSE. 2017. Review of Vapour Cloud Explosion Incidents.
http://www.hse.gov.uk/research/rrhtm/rr1113.htm
10. Wikipedia. Esso Longford gas explosion.
- https://en.wikipedia.org/wiki/Esso_Longford_gas_explosion.
11. National Fire Protection Association. NFPA 59A Standard for the Production, Storage, and Handling of Liquefied Natural Gas (LNG) 2016 Edition
- https://www.nfpa.org/
12. British Standards Institute. BS EN 1473:2016 Installation and equipment for liquefied natural gas. Design of onshore installations https://www.bsigroup.com/
13. Society of Gas Tanker and Terminal Operators. (SIGTTO).
- http://www.sigtto.org/publications/publications-and-downloads
14. Rath, S. and M. Krol. 2013. Comparative Risk Assessment for Different LNG-Storage Tank Concepts. Chemical Engineering Transactions. VOL. 31, 2013.
http://www.aidic.it/cet/13/31/018.pdf
15. Society of Gas Tanker and Terminal Operators. (SIGTTO). 2015. Guidance for the prevention of rollover in LNG tanks.
- http://safety4sea.com/wp-content/uploads/2015/07/SIGTTO-LNG-Ships-Rollover-Prevention-2012.pdf
16. IMO Press release on the phaseout of heavy fuel oils in the Arctic.
- https://eia-global.org/press-releases/mepc-70-imo-phase-out
17. International Maritime Organisation. 2016. International code of safety for ships using gases and other low-flashpoint fuels.
- http://www.imo.org/en/Publications/Documents/Newsletters%20and%20Mailers/Mailers/I109E.pdf
18. Umm Said LPG Tank Failure Qatar 1977. https://www.scribd.com/doc/21090127/UMM-Said-LPG-Plant-Disaster-03-04-77
Gyenes, Z., Wood, M-H., and Struckl, M. 2017. Handbook of scenarios for assessing major chemical accident risks. EUR 28518 EN.
doi: 10.2760/884152.
https://minerva.jrc.ec.europa.eu/en/shorturl/minerva/lup_guidepng
PDF Version for printing
Liquefied Petroleum Gas (LPG) and Liquefied Natural Gas (LNG) sites
Go back to the Common Inspection Criteria website
Now available: Handbook of Scenarios for Assessing Chemical Accident Risks
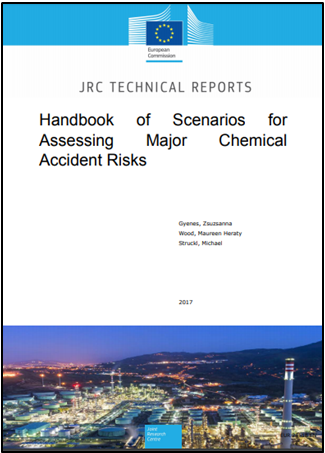
This report presents the collective work of the European Working Group on Land-Use Planning and discusses the activities towards more consistent land-use planning decisions through more understandable risk assessment approaches and data. The purpose of this book is to assist the EU Member States, especially those which do not have a consolidated system of approach, scenarios and criteria to assess the Land-Use Planning cases, in complying with the requirements of the Seveso Directive.
All JRC-MAHB publications can be found at https://minerva.jrc.ec.europa.eu/en/shorturl/minerva/publications